

Standing in front of the large AFP system in Spirit’s R&D facility, he added, “This machine can deliver with a very affordable price probably better than what they can do themselves.” Formerly Spirit’s CFO, Anderson assumed his current position in 2013 and was tasked with increasing the company’s defense work. “I can supply the prime contractors structure,” explained Phil Anderson, Spirit’s senior VP of defense and contracts in a 2014 article by The Wichita Eagle. The fuselage is most likely made using automated fiber placement (AFP).

The first fuselage is now at Bell’s Amarillo, Texas facility undergoing final assembly. Flail claims there are only three hard shims used in the whole fuselage, which he says features composite skins over metal frames.
#V 280 VALOR COCKPIT MANUAL#
Determinant assembly involves designing components that will fit together at predetermined junctions, within tolerance, in order to eliminate manual measurements, adjustments and fixturing. Other high-speed enablers were determinant assembly and laser alignment. According to Bell V-280 program director Keith Flail, design-to-delivery of the first fuselage took Spirit just 22 months and required minimal tooling. Spirit AeroSystems (Wichita, KS, US) is building the V-280 composite fuselage. SOURCE: (top) Spirit AeroSystems, (bottom) The Wichita Eagle. Phil Anderson, senior VP of defense and contracts at Spirit AeroSystems, says the company 's automated fiber placement machines deliver cost-effective, large carbon fiber parts. Spirit AeroSystems designs and builds the composite cabin and cockpit for the V-280. The group also has facilities in Derby, Portland and Yeovil, UK. Owned by The Edgewater Funds and Acorn Growth Companies, AGC produces custom, weight-saving composite structures for legacy weapon systems, composite details and assemblies for aircraft currently in production, precision exotic metal assemblies for aircraft engines, and aircraft structural fusion welding (ASFW) on alloy metal parts for aftermarket spare programs. These include the Hayden, Idaho site that was previously Unitech Composites (acquired by AGC in 2007), and the AGC Aerospace and Defense headquarters in Oklahoma City, Oklahoma. According to Rick Armstrong, AGC president and CEO, the fairing’s development was a collaborative effort between the company’s US facilities. It features an advanced hybrid composite aluminum and titanium structure covered with external composite skins, with composites making up ≈50% of its weight.ĪGC Composites and Aerostructures (Oklahoma City, OK, US) is manufacturing the over wing fairing. The company also produces the CH-53K helicopter aft transition unit, a complex fuselage section comprising over 1,000 parts and measuring 6m long by 3m wide and 3m high.
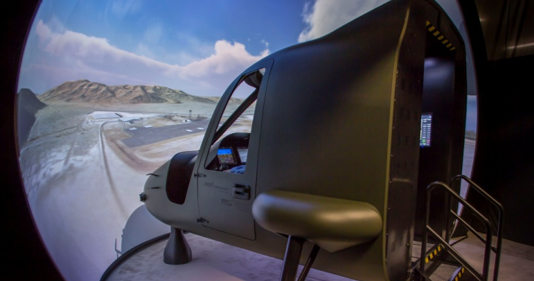
The first V-tail is scheduled to be mated to the fuselage in early 2016. GKN (Redditch, UK) is using a combination of metals and composites to produce the V-tail structure and ruddervators, which are designed to provide advanced maneuverability and control to the airframe. However, similar to the original aims of the F-35 Lighting II Joint Strike Fighter, the multiple platforms envisioned in the FVL family are being designed not to simply replace older helicopters – but also to take on missions that were previously impossible thanks to the expected range, speed and integration of high-tech systems. In consideration since 2004, FVL is a path toward replacements for the Army’s UH-60 Black Hawk, AH-64 Apache, CH-47 Chinook and OH-58 Kiowa helicopters, and the Navy’s MH-60 Seahawk. The Future Vertical Lift (FVL) program aims to develop new, faster and more agile vertical takeoff and landing (VTOL) aircraft for all of the US armed services in four different sizes: light, medium, heavy and ultra. SOURCE: Bell Helicopter V-280 Valor brochure. The Joint Multi-Role (JMR) Technology Demonstrator (TD) will mature technologiesĪnd help refine requirements for the Future Vertical Lift (FVL) program.
